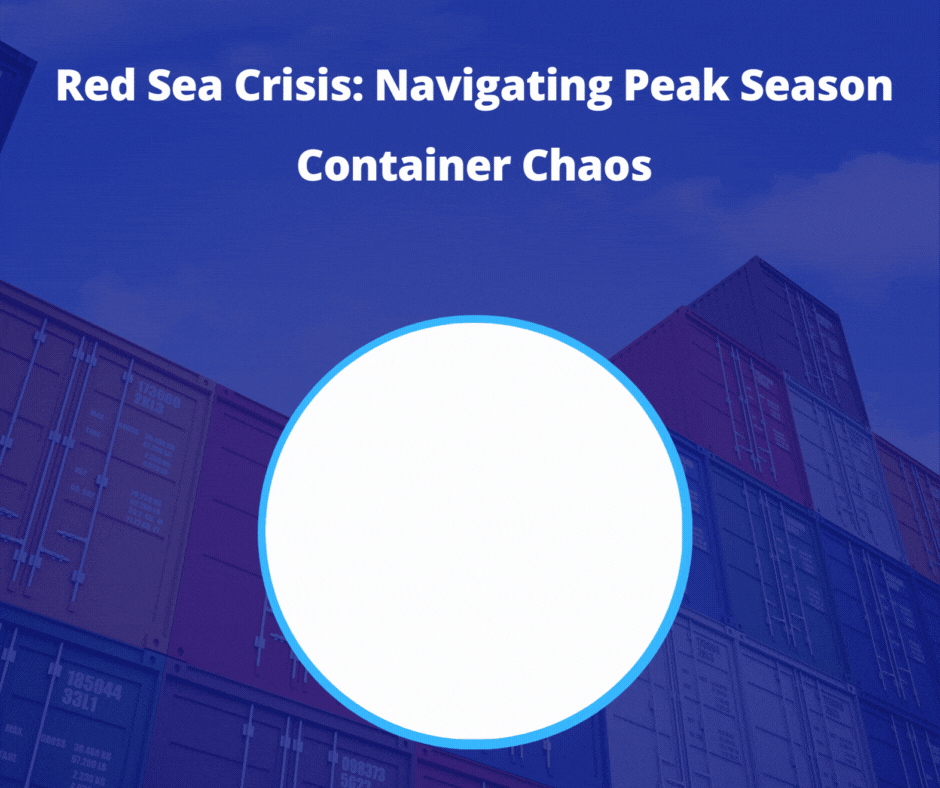
Do you have a container plan?
In the ever-evolving landscape of global logistics and shipping, the recent challenges posed by the Red Sea crisis have prompted a reevaluation of strategies, especially as the industry approaches its peak season. With disruptions altering traditional routes, logistics professionals are faced with navigating through increased transit times, fluctuating freight rates, and the critical issue of container availability. This article explores the multifaceted implications of these challenges for the logistics industry, offering insights and strategies to mitigate impacts and sustain operations effectively. By understanding these dynamics, companies can better prepare for the uncertainties of peak season and beyond.
Understanding the Crisis: Implications for Container Availability
The strategic importance of the Red Sea as a maritime route cannot be overstated. It serves as a vital conduit for international trade, particularly between Europe, Asia, and the Americas. The recent crisis and subsequent diversion of shipping routes around this pivotal region have significantly disrupted the usual flow of goods, with far-reaching implications for the global logistics industry. These disruptions have extended transit times and precipitated a domino effect impacting container availability, freight rates, and, ultimately, the efficiency of the global supply chain.
Extended Transit Times & TEU Mile Increase
The diversion has led to an average increase in transit times by several days or weeks, depending on the specific routes and destinations. For instance, voyages that previously passed through the Suez Canal are now taking longer routes around the Cape of Good Hope or through alternative maritime corridors, adding substantial mileage to their journeys. This detour has resulted in a 16% increase in global twenty-foot equivalent unit (TEU) miles—a standard measure of a ship’s cargo-carrying capacity. To put this into perspective, if the global fleet previously covered 100 million TEU miles to deliver the same cargo volume, it now has to cover 116 million TEU miles for the same task, imposing a significant strain on available capacity and operational efficiency.
Impact on Container Availability
The extended time containers spend in transit directly affects their turnover rate by slowing down the cycle of emptying and refilling with new cargo. This slowdown is critical during peak seasons when demand for containerized transport skyrockets. For logistics managers, this means needing to grapple with the challenge of securing enough containers to meet their shipment schedules, particularly for imports into the U.S., where demand remains robust.
Since the average container trip length has increased, containers are now in transit for more extended periods. This situation exacerbates the already pressing issue of container shortages experienced in various parts of the world. Before the crisis, the global supply chain was already under strain due to the pandemic-induced fluctuations in demand and supply imbalances. The current prolongation of transit times further tightens the availability of containers, compelling logistics managers to seek alternative strategies to ensure they have the necessary capacity for their cargo.
Strategies for Mitigating Impacts
To combat these challenges, logistics managers are adopting several strategies, including:
- Advance Booking and Planning: Companies are planning their shipments well in advance to secure container space, with some opting to book space up to several months ahead of their desired shipping date.
- Diversification of Supply Chain Routes: Firms are exploring alternative routes and ports to bypass congested or problematic areas, even if it means incurring higher costs or longer transit times in the short term.
- Utilizing Different Container Types: Some shippers are using non-standard container sizes (such as 45-foot containers) that may be more readily available, albeit at potentially higher costs, to mitigate the shortage.
- Investing in Container Assets: Certain large shippers are also investing in their own container fleets to reduce dependency on equipment availability.
Navigating Freight Rate Fluctuations
The Red Sea crisis has disrupted traditional shipping routes and exerted upward pressure on freight rates globally. It particularly affects shipments from the Far East to the United States. Thus, it is appropriate to explore the dynamics behind these fluctuations, their implications for logistics managers, and strategies to navigate this volatile environment effectively.
Dynamics Behind Freight Rate Increases
Various factors influence freight rates, including supply and demand dynamics, fuel prices, and geopolitical events. The diversion of shipping routes due to the Red Sea crisis has introduced additional operational costs for carriers—longer routes mean higher fuel consumption, increased wear and tear on vessels, and extended use of crew resources. Additionally, the longer transit times reduce the turnover rate of ships and containers, effectively tightening the supply of available shipping capacity.
In the weeks and months following the onset of the crisis, freight rates from the Far East to the East and West Coasts of the United States have surged. For example, rates have seen increases upwards of 145.5% for East Coast destinations and even higher, at 186.2%, for West Coast ports. This spike reflects the immediate impact of reduced shipping capacity, extended transit times, and the market’s anticipation of ongoing disruptions.
Implications for Logistics Managers
For logistics managers, these rate increases pose significant challenges. Higher freight costs impact the overall cost of goods sold, potentially squeezing margins or forcing companies to pass these costs onto consumers. In a competitive global market, balancing cost efficiency and reliable service is more critical than ever. The tightening of container availability further compounds the issue. As carriers prioritize routes and shipments based on profitability and operational feasibility, logistics managers may find securing space at reasonable rates increasingly difficult, especially during peak shipping seasons.
Strategies to Mitigate Impact
To navigate these challenges, logistics managers can employ several strategies:
- Multicarrier Strategy: Engaging with multiple carriers provides flexibility and bargaining power. By diversifying their carrier mix, companies can mitigate the risk of capacity shortages and capitalize on competitive rate offerings.
- Contract Negotiations: In contract negotiations with ocean carriers, logistics managers should consider incorporating clauses that provide flexibility in routing and capacity guarantees. Long-term contracts might offer better rates and priority loading, which is crucial in tight market conditions.
- Freight Rate Hedging: Some companies use financial instruments to hedge against sudden increases in freight rates. Though not suitable for all, hedging can provide cost stability in volatile markets.
- Alternative Transportation Modes: Exploring alternatives to ocean freight, such as rail, air, or a combination of multimodal solutions, might offer cost-effective and timely options, especially for time-sensitive shipments.
- Efficiency in Supply Chain Management: Streamlining supply chain operations can offset some of the increased costs. Consolidating shipments, optimizing inventory levels, and improving load planning can lead to significant savings.
The Long-Term Outlook: Transit & Consumer Demand
With no immediate resolution to the Red Sea situation in sight, companies must brace for extended diversion routes, possibly lasting through the first half of the year or longer. This extended transit time requires incorporation into supply chain planning to avoid disruptions. Additionally, a steady growth in consumer demand, particularly in the U.S., indicates a potential increase in import volumes, further impacting container availability and distribution strategies. Logistics professionals must remain agile, leveraging data and insights to anticipate shifts in demand and adjust their strategy accordingly.
Strategic Container Management & Repositioning
In light of the extended transit times, the concept of containers as “floating warehouses” has emerged. This implementation emphasizes the importance of strategic container location over sheer numbers. The repositioning of containers represents a significant cost, contributing to freight inflation and necessitating a more strategic approach to container management. Companies must explore innovative solutions, such as collapsible containers, to mitigate these costs and enhance the efficiency of container utilization and repositioning.
Wrapping Up
As the logistics industry navigates through the challenges posed by the Red Sea crisis and prepares for the peak season, the importance of strategic planning, flexibility, and innovation has never been more pronounced. By understanding the implications of extended transit times, freight rate fluctuations, and consumer demand patterns, logistics professionals can devise strategies to ensure their operations’ resilience and continuity. Through proactive planning and the adoption of innovative solutions, the logistics industry can overcome these challenges, maintaining the flow of trade in an increasingly complex global landscape.
One Comment on ““Red Sea Crisis: Navigating Peak Season Container Chaos””
Thank you Nelson. Your updates are very helpful indeed. Keep me posted please.