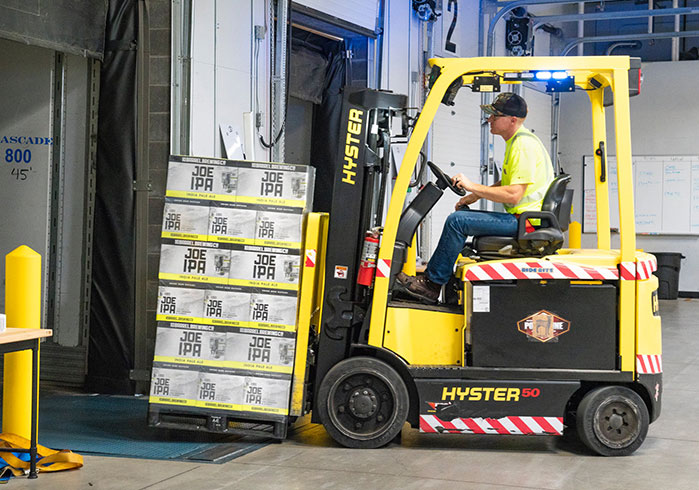
Generally speaking, e-commerce has boomed during the COVID-19 crisis, in part because consumers are less willing to shop in person and instead turn to the internet to acquire their needs. However, there has been a downside for businesses having to meet increased customer demands in a limited period of time.
One aspect of e-commerce the crisis affected was order fulfillment. As orders swelled, particularly during the early days of the crisis, many online retailers were unable to keep up which led to significant delays.
From an operational point of view, the 2020 holiday season was more difficult than usual because businesses had to deal with the reality of limited carrier capacity which reduced their speed in processing orders. The holiday season is already typically frenzied with an influx of orders and deliveries, but the lockdown situation only made things more chaotic.
How Order Processing Increased During the Pandemic
The public healthcare crisis created specific pressures and requirements when processing orders. Global supply chains were clogged by a short-notice desire to stock up on goods to meet the anticipated rise in demand. Once the COVID-19 outbreak started in Wuhan (China), many factories closed, which greatly impacted the supply chain worldwide.
Amazon warehouses were overwhelmed for a time, which meant the company limited what it was shipping to goods considered to be essential. FBA merchants were unable to access the kind of shipping services that they needed and could not easily fulfill the orders that had been put through. Online orders spiked, but the industry seemed unable to respond quickly enough.
In order to improve the performance on this front, many companies implemented new processing protocols. At the same time, the companies were concerned about ensuring that all employees who were involved did not become exposed to infection. The work of carriers like UPS and FedEx was essential in the order-fulfillment process.
As 2020 reached its midpoint, order processing had achieved equilibrium as many fulfillment centers started to adapt to the new demand patterns. The fall of 2020, however, introduced additional problems including slowdowns. The US election in November created additional strain on the USPS which led to delays that became the new normal as the country entered the holiday season. In response, FedEx and UPS reduced limits on the number of packages that any customers could pick up. Inevitably, the rationing of delivery capacity created chaos throughout the holiday season.
How Limited Carrier Capacity Impacted Supply
One of the key factors to consider in shipping scheduling is the possibility of “limited carrier supply.” Typically, this happens through a third-party logistics company or 3PL. Indeed, some have argued that it is used as an excuse for internalized inefficiency on the part of the courier and supplier. Nevertheless, it is important to acknowledge the fact that limited carrier capacity actually affected suppliers and shippers in 2020.
As the U.S. became the epicenter of the COVID-19 pandemic, many consumers decided to switch to online shopping. Suddenly, UPS and FedEx were delivering items that were previously bought in person. The items included medical supplies, gifts, and even groceries. The volume of products that required processing was higher than the maximum capacity that the industry was ready to offer, and the holiday season escalated matters further.
High-volume shippers were the most affected by these changes. This led to a rationing of deliveries on any given day and for any given customer. Inevitably, backlogs started to appear. Some sought alternative solutions from providers such as USPS. That particular provider had also sustained a shortage in staff and funding under the presidential administration, which was ramping up for an election year. An already struggling situation then had to deal with an influx of new customers in addition to its already over-stretched client list.
How Are the Major Carriers Involved?
All three major US carriers – USPS, FedEx, and UPS – had a role to play in stepping up to make adjustments to their processes during the backlog of orders in 2020. In order to better understand how these companies played a role, we have to examine the six general steps for fulfilling an order:
- The customer arranges for an inventory to be shipped to their processing warehouse.
- The warehouse then logs all the products before storing the stock.
- The order is relayed from one of the selected e-commerce platforms before moving to the fulfillment center.
- The order processing formally starts with operations personnel picking up all the items that comprise the order that was made by the customer. These are then placed in a packaging station for processing and labeling before shipping.
- The selected carrier picks up the order. In this case, the package is placed at the nearest sorting center for distribution. The protocol tends to favor the city that is closest to the final destination for the package.
- Finally, a delivery driver places the order at the doorstep to complete the circle.
Throughout this process, USPS, UPS, and FedEx played – and continue to play – a critical role as the biggest carriers currently operating in the U.S. It is through these carriers that the customer is linked to the supplier within set parameters such as time and quality. Timing is of the essence at each stage. For example, orders must be relayed from the sales platform to the 3PL as soon as possible so that they can be processed right away.
Some companies offer same-day fulfillment packages that create a maximum window of 24 hours between when the customer ordered and when it arrives on their doorstep. Customers tend to complain if there are delays and may even choose an alternative provider. In setting delivery times, the shipping zone is of the essence. These are calculated by comparing the distance traveled from the fulfillment center to the customer’s address.
During the second part of 2020, these time limits were overly stretched. Although many merchants had very limited control over the causal factor, they nevertheless were the ones so ultimately sustained customer blame. This led to a backlog of customer care issues and complaints.
How to Reduce Order-Processing Delays
Any business that wishes to retain good customer relations must ensure to reduce delays in delivery. In particular, customers that rely on e-commerce are very sensitive to time delays. The first response is to communicate early and often about the global issues so that customers are aware that there may be delays. This gives them an opportunity to find alternatives if they cannot wait. For example, in the early days of the pandemic, some companies introduced warning banners at the top of their e-commerce platforms which have now become a regular element of e-commerce websites in 2021.
Try to under-promise and over-deliver rather than the opposite. This means the customer is not faced with unrealistic expectations that you are bound to disappoint. Even where there are hiccups along the way, make sure that the customer is always kept in the loop.
Ensure that you develop a good working relationship with your fulfillment company, especially because it yields more influence in the industry than an individual retailer. Discuss volume implications and the possibilities of compromises or exceptions.
Looking Ahead to Order Processing in 2021
Now that 2020 is behind us, it is important to plan a more effective approach for processing orders in 2021. The one thing that will remain constant is the unpredictability of the market. We anticipate that the peak shipping that started in the second half of 2020 will continue this year. Moreover, e-commerce is likely to remain a fixture, and volumes will continue to increase. Perhaps an advantage, though, is that the experience from 2020’s global crisis can offer insight into how to better prepare for the future.